电液推杆的定义与应用场景
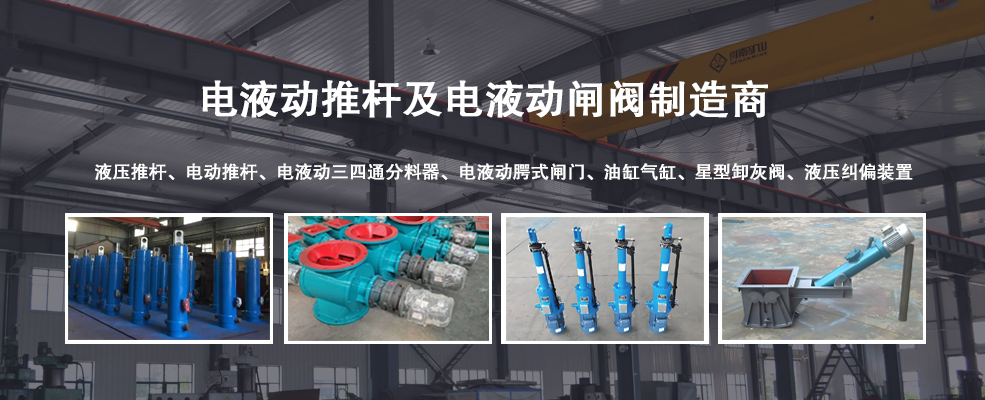
电液推杆是一种将电能转换为液压能,再通过液压推动活塞进行直线运动的驱动装置。它集成了电机、液压泵、液压缸等核心部件,具有结构紧凑、功率密度高、输出力大等特点,广泛应用于矿山机械、冶金设备、交通运输、自动化生产线等领域。
在工业自动化快速发展的背景下,电液推杆因其出色的负载能力和灵活的控制特性,成为执行机构中的重要组成部分。它能够在恶劣环境中长时间稳定运行,并且可以根据需要调节推力、行程和速度,满足各种复杂场景的需求。
电液推杆设计要点解析
结构设计的可靠性与耐用性
电液推杆的设计必须兼顾承载能力和使用寿命。推杆的主要结构包括液压缸体、活塞杆、密封件和电机联动装置,其中每个部件的材料选择和加工精度对整体性能都有重要影响。例如:
缸体材料:通常选用高强度合金钢或耐腐蚀不锈钢,以应对高压和恶劣环境。
密封系统:优质的密封件不仅能够防止液压油泄漏,还能增强设备耐用性,常用材质包括聚氨酯和氟橡胶。
液压系统的优化设计
液压系统是电液推杆的核心,直接影响其运行效率与控制精度。在设计时需关注以下几点:
液压泵选择:高效、低噪声的液压泵可以提升能源利用率,常见的有齿轮泵、柱塞泵等。
油路优化:合理布置油路并减少弯曲点,有助于降低压力损耗。
控制阀配置:配置比例阀或伺服阀,以实现精准的推杆控制,满足多样化工业需求。
力学性能的计算与校核
电液推杆的推力、行程和速度是其核心性能指标,必须通过理论计算与仿真校核予以保障。例如,针对高负载工况,可采用有限元分析法评估结构变形和应力分布,确保安全裕度。还需合理设计推杆导轨和缓冲结构,减少运动过程中的振动和冲击。
电气控制的智能化设计
工业4.0的推进,电液推杆的控制系统逐渐向智能化方向发展。可通过集成PLC或嵌入式系统,实现精确定位、速度调节及故障诊断功能。无线监控与远程操作技术的应用,也使得电液推杆的操作更加便捷。
案例解析:某冶金设备中的电液推杆应用
以一套冶金液压门驱动系统为例,该系统要求电液推杆具备强力输出和高精度控制功能。通过优化结构设计和液压回路,该推杆实现了100吨级推力输出,控制误差小于1毫米,大幅提升了设备工作效率和稳定性。这一案例充分体现了电液推杆在重载场景中的独特优势。
电液推杆的制造工艺要点
制造工艺是电液推杆性能稳定的基础,以下为关键工艺步骤的详细解析:
核心部件加工与装配
电液推杆的液压缸体和活塞杆是最重要的部件,其加工精度直接决定推杆的运行平稳性:
缸体加工:采用高精度内孔镗削和外圆磨削工艺,确保液压缸内壁的表面粗糙度达到0.8μm以下,减少内泄漏和摩擦。
活塞杆加工:采用淬火处理和电镀工艺提升强度与耐磨性,表面镀铬厚度控制在20-40μm之间,以保证其耐腐蚀性能。
密封与焊接技术
密封安装:在密封件的安装过程中,需特别注意防止刮伤和变形,常用装配工具包括橡胶锥和辅助导向器。
焊接工艺:推杆外壳的焊接采用自动化激光焊接或氩弧焊,以确保焊缝的强度和气密性,避免液压油渗漏。
液压油与系统清洗
高品质的液压油是电液推杆长效运行的保障,在灌注液压油之前,必须对整个液压系统进行严格清洗:
清洗步骤:使用高压循环泵进行多次冲洗,直至管路内无杂质残留。
油品选择:选用黏度合适的液压油,添加抗氧化、抗磨损添加剂以延长系统寿命。
性能测试与质检
在电液推杆完成装配后,需进行全面的性能测试与质量检验,包括:
静态测试:检查密封性和推力是否达到设计值。
动态测试:评估推杆在高频启停、负载变化情况下的响应速度与稳定性。
环境测试:模拟高温、低温、粉尘等恶劣环境,验证推杆的耐久性和可靠性。
展望:电液推杆的发展趋势
智能制造与绿色环保理念的普及,电液推杆正向着高效、节能、智能化方向发展:
新能源设备:电液推杆在光伏发电、风力发电中的应用日益广泛,可用于调节角度和位置,提高发电效率。
轻量化设计:采用复合材料替代传统金属部件,降低重量的提升抗腐蚀性能。
智能反馈技术:集成传感器与AI算法,实现实时监测与故障预测,提升运维效率。
总结
电液推杆作为现代工业不可或缺的关键部件,其设计与制造贯穿了材料科学、机械工程和智能控制等多学科知识。通过不断优化设计与提升制造工艺,电液推杆将在更广泛的领域中发挥重要作用,为工业自动化提供更高效可靠的解决方案。